Why GROSIZE-200 and not Native Maize Starch?
In many paper mills Native Maize Starch is used for web sizing and surface sizing. But Oxidized Starch has many advantages over Native Maize starch in paper making process.
In industrial water-borne coatings applied at high shear rates the molecular weight of native starch has to be reduced in order to achieve sufficient low viscosity of the starch solution. This can commonly be performed by oxidation, which is a degrading process. Native starch has a very high viscosity at high starch concentrations whereas the viscosity of degraded starch is not greatly affected by an increase in concentration. This makes oxidized starch easier to use than native starch at higher concentrations. The oxidation process is mild and is performed under controlled conditions, and this allows the oxidant to attach to the most reactive bond on the starch polymer.
The gelatinization temperature of the starch is reduced in proportion to the degree of oxidation. The granules disintegrate when cooked and this results in a reduction in the peak viscosity. All these properties make oxidized starches suitable as paper coating binders and in addition, the anionic character of oxidized starches prevents agglomeration of pigments in coating formulations.
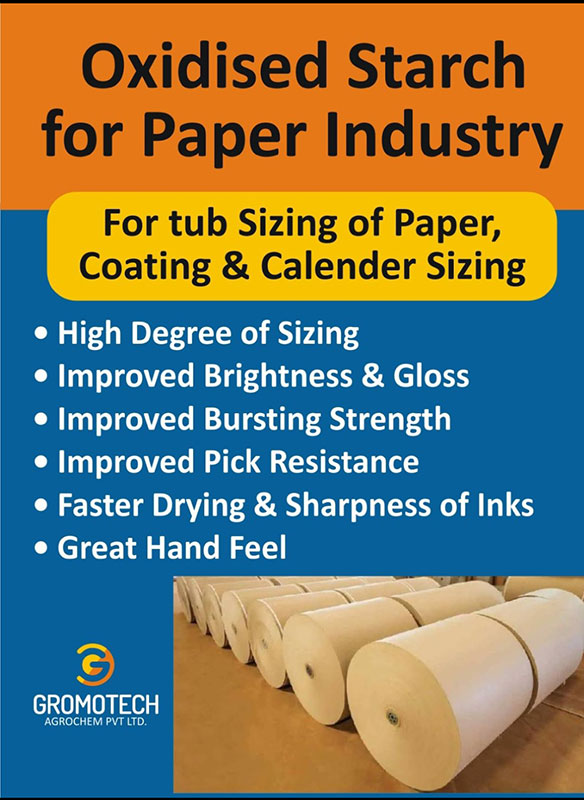
GROSIZE-200 (Oxidized Starch) in the surface treatment of paper & board
In papermaking, starch is the third largest component by weight, surpassed only by Cellulose fiber and mineral pigments. This makes the GROSIZE-200 one of the most important raw material for the paper industry.
The main application areas for starch within the papermaking process are-
Furnish preparation prior to web formation
– GROSIZE-200 is used as a flocculating agent and retention aid, and to improve internal sheet strength.Surface Sizing
– GORSIZE-200 is used as an adhesive to bond vessel segments and loose Fibers at the sheet surface, to enhance paper strength and stiffness, to give dimensional stability & improve offset printabilityCoating
– GROSIZE-200 is used as a binder for pigments.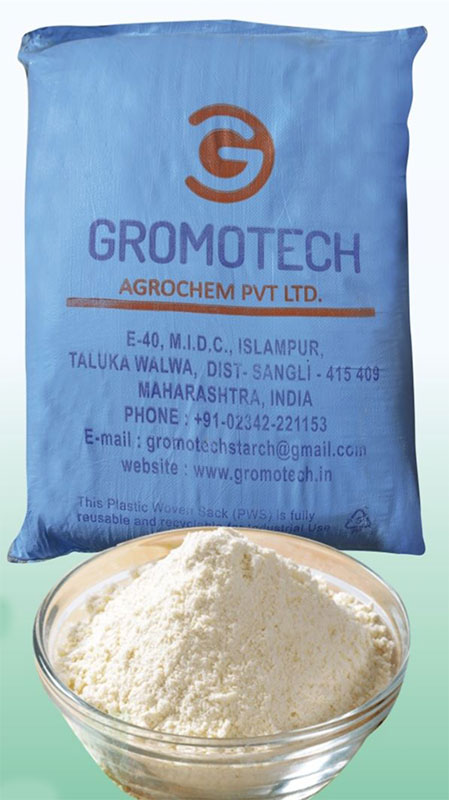
Surface treatment - Sizing & Coating
Most grades of paper and board need to be resistant to wetting and penetration by liquids. The properties of the final paper surface can be modified in several different ways, the most important being surface sizing, coating and calendaring by GROSIZE-200.
Surface Sizing
Surface sizing is a process whereby chemical additives are applied to provide the paper with resistance to wetting and penetration of liquids, i.e. make it more water repellent and to bind the particles in the surface and increase the surface strength. Internal sizing is a process where chemicals are added to the paper stock and retained on the fibers in the wet end. Surface sizing is the application of a size to the web surface at the dry end of the process. GROSIZE-200 is used as binder in surface sizing. Besides raising the surface strength, starch addition also lowers water sensitivity, reduces dimensional changes, imparts stiffness, and raises air-leak density of the sheet and it also improves the tensile strength and internal bonding of the paper.
Surface Treatment
A paper surface sized by the application of GROSIZE-200 resists penetration of water over a relatively long period of time despite its hydrophilic character. However, the application of a GROSIZE-200 improves the resistance to water. GROSIZE-200 is resistant to retro gradation and their dispersions can be held at a lower temperature than is required for the products of chemical or thermal/chemical conversion. GROSIZE-200 is used for surface sizing of paper and paperboard at the size press machine for increasing the mechanical strength, including the strength of the surface, and also as a bonding additive in the manufacture of drywall. GROSIZE-200 is commonly used to provide water-resistance (prevent paper from blurring with water or ink) and printability to paper by surface application.
Adavantages
- Improved paper appearance with respect to brightness, gloss, smoothness of paper.
- Faster drying of inks and sharpness of print on paper.
- Can be used when a high degree of sizing is required.
- Great hand feel.
- Provides additional starch/ cellulose hydrogen bonds resulting in improved bursting strength.
- Improves the pick resistance property of paper.
Typical Analysis
Characteristic | Property |
---|---|
Color/ Form | White to off-white powder |
Moisture % | 12.00, Max. |
Ash % | 3.00, Max. |
Viscosity of 10 % solution cooked: At 90O C and checked at 50O C in Cps in B.F. Viscometer | 25-35 |
Brightness % (on Elrepho) | 85.00, Min. |
pH of 10 % solution | 5.50 – 6.50 |
Method of Use
The product at a required concentration is mixed with cold water under agitation to form homogenous slurry. The slurry is cooked by means of jet cooker or steam heated jacketed vessel with agitation at 90O C for about 20 minutes. The cooked paste can be directly added to the size press at a desired dose.
Packaging
GROSIZE-200 is available in 50 kgs net HDPE bag with polyethylene liner inside.PLEASE CONTACT US FOR YOUR SPECIFIC QUALITY REQUIREMENTS.
Get in Touch With Us
Frequently Asked Questions
Corrugated paper box is used mainly for shipping / transportation and storage of variety of items for their strength and durability. In the process of making box mainly paper and gum adhesives are major players which determine strength of the box. More moisture in the box will cause lower compression strength of the box. Lower compression causes collapse of stacked boxes and thus damage to the goods packed inside.
So control of moisture in corrugated box means controlling moisture in paper and in gum adhesives used in box making.
1.Controlled moisture in paper.
The major component of paper, cellulose fiber, is hygroscopic in nature and therefore tends to absorb moisture from a damp or humid atmosphere or release moisture in dry atmosphere. When paper gains moisture corrugated box loses its bursting strength (BS) and compression strength (CS) and when it loses moisture corrugated box develops the cracking or board breaking problem.
To avoid this cracking of corrugated sheets use of sprayer to spray water onto base paper, changing of machine speed and adjustment of the flexible paper-lead roller to cut preheat area are required. Avoid exposure of paper reels in open sun heat which will bring down paper moisture substantially to cause cracking of corrugated sheets at the end.
To overcome excess moisture in corrugated board use of correct paper cob, changing machine speed, use of preheaters etc. are some of the solutions.
2. Moisture control through gum adhesives
Gum adhesives play major role in avoiding excess moisture in corrugated box. Type and quality of starch used in adhesives, type of fillers used, modifications to starch and chemicals used in the gum adhesives are major players in causing excess moisture in corrugated board.
a) Gel temperature of gum is important in automated plants and in single face. High pin adhesion at low temperature gives complete dry liners and board. If gum fails to get gelatinized immediately when it reaches heaters at the set speed of machine, it fails to develop stronger bond adhesion and develops the tendency of gaining moisture from atmosphere in later stage even after complete drying.
b) Type of starch used and specific modification to starch to develop moisture resistance are very important factors. Usually hydrolysis of starch with the use of acid and then use of strong alkali to get viscous gum is a common product which is available in the market. These type of adhesives are bound to gain moisture in damp atmosphere and humid climatic conditions. Special modification treatment to high quality starch to develop moisture resistance is required.
c) Different fillers are used in gum adhesive making to bring down cost and make our adhesives cheaper in the market of competition. Very low cost fillers such as different flours, clay, Urea etc. are used which pay no role in gum quality than reducing price substantially. Flour, clay or urea are more of hygroscopic in nature and cause more and more moisture gain whenever gets opportunity.
d) Chemicals used in gum adhesives such as Sodium Hydroxide (caustic soda) is highly hygroscopic and not only absorbs moisture but carbon dioxide, sulfur dioxide in the air. It is also highly deliquescent and absorbs moisture to form an aqueous solution. More moisture means lesser bursting and compression strength which results in collapse of stacked boxes.
Grodex Moisture Resistant Powder adhesives are made of finest quality of different types of starch. A unique modification process with the state of art technology develops complete moisture resistance in adhesives. These products are not only Sodium Hydroxide (caustic soda) free but no other chemical is used in it make it eco and worker friendly. These are proved adhesives for moisture resistance all over the world over past several years for guaranteed moisture resistance and control in corrugated paper board industry. Use of these adhesives will solve not only your moisture problems but will provide you totally new thinking line of grabbing huge hidden profits from your box in a very competitive market.Only paper, how superior quality is, without corrugation process can’t give stacking strength for storage and transportation of different goods and therefore flute formation and adhesives applied to both the sides of flutes, determines strength of corrugated box. If these gum lines starts absorbing moisture from air, box starts losing its compression and collapses on stacking.
Therefore moisture resistance of gum lines on the paper from both the sides of flute is essential to guarantee unchanged compression strength of corrugated box. Fast drying of corrugated sheet and its moisture resistance are two different concepts. Gum which is drying fast need not have moisture resistance and vice a versa.
Major problems caused due to moisture gain in box
- Box loses its compression strength and collapses in stacking position
- Warp (bending of corrugated sheets) due to excess moisture.
- Chances of fungus on the surface of box as moisture provides dampness and required temperature for development of fungus.
- Rusting of stitching pins.
- Corrugator starts using higher grade papers to achieve desired strength which eats profit which has already narrowed due to tough completion.
Advantages of good quality moisture resistant adhesives
1. Guaranteed permanent compression and bursting strength in any climate conditions and even in export of goods when box travels offshore in deep sea where relative humidity goes very high.
2. Excellent finish, great feel to bare hand and improved aesthetics of box.
3. No chance of fungus as gum adhesive resist moisture and keeps surface dry.
4. No chance of pin rusting as gum adhesive remain dry after complete drying.
5. Bursting and compression strength of box improves substantially. This helps corrugators to save in terms of paper by using lower grades instead of higher grade papers. Paper cost consists of almost 97% of total box cost. Savings in paper means saving in 97% cost of box. Thus corrugator gets an opportunity to grab huge hidden profits by using quality gum adhesives. More margins helps him to become more competitive in the market and better quality and improved aesthetics of box helps him fetch more orders in open market, which further increases market share with improved margins.
Grodex moisture resistant powder adhesives are guaranteed proved moisture resistant and helps corrugators to mint money in highly competitive market.
Moisture resistance of box and waterproofing of box are two different concepts. Moisture resistance is applicable only in damp conditions or humid climate where as water proofing is applicable only when box comes in direct contact with water.
Humid air has a density of approximately 1.225 kg/m³ and density of water is 997 kg/m³. Gum lines of moisture resistant grade powder adhesives can on can resist moisture due to its very low density but can’t resist direct water due to its very high density. When box comes in direct contact with water not only gum but even paper starts absorbing it and thus collapse.
So what is important is moisture resistance and not waterproofing of gum adhesive. Stacked box should stand in any climatic condition and not in water. If at all waterproofing is demanded then coat of waterproof chemical is applied to paper. Always go for moisture resistant grade adhesives though costly as they prove to be highly profitable in actual practice.
Fungus mold is everywhere. There is realistically nothing you can do to stop mold spores from being on your box. They're everywhere. As soon as a door or window is opened, mold spores come in. As soon as you enter your factory, mold spores that were on you are now in your factory.
How mold germinate from spores and grow (Dust/moisture/temperature)
Mold consumes just about anything organic including things like dust. No matter how clean you try to keep your factory, there will be always still be some dust in it. So, other than keeping a relatively clean factory, mold's food source is something that is very hard to control.
Moisture source is the most controllable source. Moisture sources can be actual moisture gain by adhesives used and high cob value papers and even humidity. Without moisture, mold cannot even start to germinate. Control the moisture and you control the mold.
Different mold species need different temperatures, but most are within the comfort levels we have in our factories. Caustic based gum used by us not only absorbs moisture but also provides temperatures which helps to grow mold. So use of Sodium hydroxide (caustic soda) based gum is what we consider an uncontrollable source.
Always use Natural Chemical free gum adhesives to avoid Fungus / mold growth in box.
Grodex moisture resistant Powder adhesives are totally Sodium Hydroxide (caustic soda) free and does not provide source for development of mold / fungus in box.
pH of the gum adhesives does not make any sense in corrugated paper board industry. Sodium Hydroxide is the main culprit which is the main cause of moisture in box. Moisture gain in box not only decreases bursting strength / compression strength but also causes fungus growth, pin rusting, wash board, warp etc.
Most of the neutral pH adhesives available in the market are sodium hydroxide (caustic) based and are neutralized by humectants like urea. Such adhesives do absorb moisture even after complete drying of box. So better insist on such adhesives which are totally chemical free and develops plasticize gum film on complete drying.
Grodex Moisture Resistant Powder adhesives are totally chemical free, made out of finest quality of combination of different starch. This adhesive gives a plasticize film of gum on complete drying which prevents absorption of moisture in it and thus ensures guaranteed permanent bursting strength and compression strength in any weather condition.
During production of corrugated boards, many have met the problems caused by inaccurate control of moisture, whether by higher (leading to collapse, flute-exposure) or lower moisture (leading to board breaking). Moisture control is a crucial issue in production and procession of corrugated boards.
Not enough water in board would make them to be crisp and easy to breakdown. But moisture control is a complex process affected by many elements.Demand conforming base paper from suppliers. Not only board but even base paper will crack if moisture level of paper is below 5%. Store base paper in separate warehouses with temperatures within 15℃ and 20℃, and relative humidity within 30% and 40%
Don’t expose base paper in the open air, otherwise the moisture of base paper would change, and moisture in the ends and middle part would vary from one another, which would make it harder for further procession.
Overheating of the single facer and hot plates is one of the reason of cracking or breaking of board. Adjustments of speed and use of water sprayer is required to maintain moisture level of board.
Warp means “corrugated sheet or box to become bent or twisted out of shape, typically as a result of the effects of heat or dampness”. Bent or twisted corrugated board results in excessive scrap, waste, and reduced production rates.
What Causes Warp?
- Moisture imbalance between the top and bottom liners
- Tension imbalance between the top and bottom liners
- Different types and grades of linerboard and inner linerboard. Generally, linerboard is better than inner linerboard.
Check following points to correct warp issue-
In the process of applying adhesive to the liners, there should be a delicate balance of heat and bonding between the layers with the adhesive consistently applied to the flute tips. Exposure to high humidity, applying excessive adhesive, inconsistent adhesive application and improper glue roll to paper speeds will all cause moisture imbalance which in turn leads to warp in the cross-machine direction.
The main technical parameters of the linerboard and inner linerboard are different. From the perspective of carton performance or the user's cost reduction, the linerboard and inner linerboard are required to be different.
Difference in Moisture content of papers due to the differences of supplier, transportation inventory and other environmental humidity. Some moisture content of linerboard are larger than inner linerboard, some are smaller.
Big difference in GSM and BF of linerboard and inner linerboard is also one of the reason of warp.
The moisture content of the same batch of paper may differ. The moisture content of one part of the paper is different from that of the other part, or the two ends of the paper, the outer edge and the inner core.
If vapor spray device is not used correctly, or there is no spray device on the machine.
If the paper after the preheating of moisture loss time is insufficient, or the environment humidity, poor ventilation, improper speed of the production line.
In a Single side corrugated machine, glue amount is improper due to uneven gum roller can cause uneven shrinkage rate of cardboard.
Techniques for reducing moisture related warp include:
- Increase corrugator speed (if possible)
- Use of proper temperature control panels to avoid excessive heat.
- In a single facer with electrical heaters, never use very high capacity heaters than what recommended by machine makers as per the size and speed of machine.
- Keep adhesive settings to minimum. More adhesive means more water which comes through adhesive.
- Equalize the temperature across the width of the sheet by inspecting for parallel misalignment between the preheater drums and wrap arms, and make proper alignment adjustments so that they are parallel one another
Tension Issues
A difference in tension between the top and bottom of the sheet can result in machine direction warp. Main reasons for this tension related warp are:
- Preheaters turning improperly (or not at all)
- Rolls not turning freely
- Inadequately functioning roll stand brakes
- Poorly maintained web guides
- Excessive drag in the hot plate section
Washboard is an undesired effect on the surface of corrugated sheet (uneven corrugation flute markings). The main reason of washboard effect on corrugated board is excess moisture retention in board and / or shrinkage of top paper due to poor quality gum adhesive.
Minimum application of high solid natural gum is must to get excellent finish to the box. If gum quality is poor, operator releases excess gum to ensure perfect lamination of top paper and this is the main reason of washboard effect on the top surface of the corrugated sheet. If viscosity of gum is too high, gum consumption will increase to cause washboard at the end. Use of Sodium Hydroxide (caustic soda) and addition of cheap fillers in gum powder such as urea, sault etc. causes shrinkage of top surface paper.
Insist gum supplier to give high solids, low viscosity and chemical free gum made of pure starch without any fillers. Quality high solid gum will give operator a confidence to release minimum possible gum. Minimum release of gum not only improves aesthetics by solving washboard but also increase overall strength of box.
Grodex moisture resistant grade powder adhesives for corrugated paper board industry are made from finest quality combination of starch, are of high solids and low viscosity. Minimum application of these adhesives give more than double the coverage than other normal gum available in the market. Grodex adhesives improves aesthetics of box substantially and are suitable even for high quality virgin imported papers where black lining is a common issue.
Let us try to understand drying process.
In summer due to dry & hot weather conditions, box dries automatically & very fast. But in rainy & winter season, it takes longer time for complete drying or in most of the cases box regains moisture even after complete drying.
In summer, we wash clothes at our home & clothes get dry within few hours, without doing anything. But in rainy & winter season clothes doesn’t get dry so easily. We have to do so many things to dry them completely. We keep wet clothes below ceiling fan & if they still found wet we apply heat by pressing them with iron.
Corrugated box is made of paper which contains wood fibers. Box will not dry automatically in humid climatic conditions. Same thing we have to do with corrugated boxes to dry them fully if we want faster drying and faster delivery.
Put them either in front of air circulator or in drying chamber to apply heat.
Now the problem starts when box regains moisture even after complete drying. Here role of gum adhesive is very important. If you want to overcome problem of moisture regain always use gum which doesn’t contain Sodium Hydroxide (caustic Soda). Caustic soda is hygroscopic and always regains moisture whenever it gets an opportunity.
Use high solids, low viscosity gum made of pure quality starch. Release minimum gum which will promote faster drying.
Grodex Moisture Resistant Powder Adhesives fast drying and give moisture resistant gum films on drying which permanently prevents regaining of moisture.
It means on complete drying -
1. b/s & c/s achieved on drying remain forever in any weather condition & even in refrigeration.
2. Box remains dry & avoids fungus growth.
3. Rusting of pins is avoided.
4. Excellent finish & aesthetic of box is achieved by avoiding warp & wash board.
With the use of low quality chemical based gum, even if you try & dry your boxes, they will gain moisture even after complete drying. But grodex adhesives resist moisture and keeps your boxes dry forever.
Stitching wire are available either Electroplated or Hot Dipped. In both the cases it is made of MS and coated to prevent rust. Such coating can delay rusting of pins but can’t avoid rusting of pins totally.
Pin gets rusted when it comes in to constant contact of water / moisture. Chemical used in gum adhesives such as Sodium Hydroxide (caustic soda) is highly hygroscopic and not only absorbs moisture but carbon dioxide, sulfur dioxide in the air. It is also highly deliquescent and absorbs moisture to form an aqueous solution. Caustic soda is also highly corrosive. Thus it promotes more moisture in the corrugated box through gum which causes rusting of stitching pins.
Always use gum without any chemicals (free of caustic soda) to overcome the problem of rusting of stitching wire / pins.
In the process of export corrugated box travels in a container in a deep sea where humidity goes very high. If gum adhesive used in such box consists of Sodium Hydroxide (caustic soda) gum lines will start gaining moisture and will cause following problems –
Drop in Bursting strength and compression strength of box resulting in collapse and loss of packed goods.
Chances of fungus on the box due to higher moisture.
Rusting of pins.
To avoid these problems always use gum adhesives which is totally chemical free and which gives guaranteed moisture resistance in any weather condition.
Grodex Moisture Resistant Powder Adhesives are totally chemical free (doesn’t contain caustic soda). Modification of starch is done with unique process with the state of the art technology which guarantees moisture resistant gum film lines after complete drying. It means box made of grodex powder adhesives gives guaranteed permanent bursting strength and compression strength even in deep sea in very high humid conditions. Moreover it improves aesthetics of box by giving great finish and no washboard issues.
Can Gum adhesives improve bursting strength and compression strength of the box?As a practice corrugators do believe that paper used in the box determines bursting and compression strength. Which is very much true.
But on the other hand gum adhesive used in the box making decreases bursting strength and compression strength of box, if low quality chemical based gum adhesives are used.
How gum plays a role –
- Type of starch used and specific modification to starch to develop moisture resistance are very important factors. Usually hydrolysis of starch with the use of acid and then use of strong alkali to get viscous gum is a common product which is available in the market. These type of adhesives are bound to gain moisture in damp atmosphere and humid climatic conditions. Special modification treatment to high quality starch to develop moisture resistance is required.
- Different fillers are used in gum adhesive making to bring down cost and make our adhesives cheaper in the market of competition. Very low cost fillers such as different flours, clay, Urea etc. are used which pay no role in gum quality than reducing price substantially. Flour, clay or urea are more of hygroscopic in nature and cause more and more moisture gain whenever gets opportunity.
- Chemicals used in gum adhesives such as Sodium Hydroxide (caustic soda) is highly hygroscopic and not only absorbs moisture but carbon dioxide, sulfur dioxide in the air. It is also highly deliquescent and absorbs moisture to form an aqueous solution. More moisture means lesser bursting and compression strength which results in collapse of stacked boxes
Problems caused due to moisture in Corrugated Box
Only paper, how superior quality is, without corrugation process can’t give stacking strength for storage and transportation of different goods and therefore flute formation and adhesives applied to both the sides of flutes, determines strength of corrugated box. If these gum lines starts absorbing moisture from air, box starts losing its compression and collapses on stacking.
Therefore moisture resistance of gum lines on the paper from both the sides of flute is essential to guarantee unchanged compression strength of corrugated box. Fast drying of corrugated sheet and its moisture resistance are two different concepts. Gum which is drying fast need not have moisture resistance and vice a versa.
Major problems caused due to moisture gain in box
Box loses its compression strength and collapses in stacking position
Corrugator starts using higher grade papers to achieve desired strength which eats profit which has already narrowed due to tough completion.
Advantages of good quality moisture resistant adhesives
Guaranteed moisture resistance and permanent compression / bursting strength in any climate conditions and even in export of goods when box travels offshore in deep sea where relative humidity goes very high.
Bursting and compression strength of box improves substantially. This helps corrugators to save in terms of paper by using lower grades instead of higher grade papers. Paper cost consists of almost 97% of total box cost. Savings in paper means saving in 97% cost of box. Thus corrugator gets an opportunity to grab huge hidden profits by using quality gum adhesives. More margins helps him to become more competitive in the market and better quality and improved aesthetics of box helps him fetch more orders in open market, which further increases market share with improved margins.
Grodex moisture resistant powder adhesives are guaranteed proved moisture resistant and helps corrugators to mint money in highly competitive market.
Grodex Moisture Resistant Powder adhesives are made of finest quality of different types of starch. A unique modification process with the state of art technology develops complete moisture resistance in adhesives. These products are not only Sodium Hydroxide (caustic soda) free but no other chemical is used in it make it eco and worker friendly. These are proved adhesives for moisture resistance all over the world over past several years for guaranteed moisture resistance and control in corrugated paper board industry. Use of these adhesives will solve not only your moisture problems but will provide you totally new thinking line of grabbing huge hidden profits from your box in a very competitive marketPowder Adhesives For Corrugated Paper Boards

Grodex Autogum
Grodex Autogum Delux is specially designed powder adhesive for Automated corrugation plants. Nowadays emergence of high speed Auto plants have compelled to go for adhesives which are specialty and can give results at low steam pressures

Grodex Cold Paste Chemical Free
Chemical free Neutral PH pasting powder Adhesive (Cold Process).Pasting Powder Adhesive for semi automatic plants.Improves B/S & C/S of box Substantially.Guaranted moisture resistence.No Fungus/No Pin rusting/No markings on imported papers.

grodex Corrogum Hd
Chemical Free Neutral PH Corrugation powder Adhesive (Cold Process).We have different grades & products in this catagory with different geletanisation points to suite application on different machines.Low viscosity -High coverage 100% dry liner from heaters. improves C/S Substantially.

grodex TiO PS
Chemical base Raw pack system powder adhesive for pasting (Cold Process).Chemical based(three pack system) adhesive for pasting of sheets in semi automatic plants. Can be used for corrugation.(Two in one) available in different water mixing ratioes 1:5 to 1:7.

grodex Hot paste
Neutral PH pasting adhesive to be used after cooking (Hot Processed).Pasting gum powder for semi automatic plant cooking at 100 degree centrigrade.is required to prepare gum. Available in different water mixing ratios from 1:3 to 1:7.